Combo Roof System
The Combo Roof System offers numerous benefits for both contractors and homeowners:
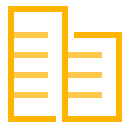
Proof Max For Building Contracting
Your one-stop shop for all of your construction needs
Why Combo Roofing System?
The strength and integrity of a roof are crucial to extending the lifespan of a building.
The overall performance of a roof depends on the quality of design, workmanship, and materials.
In the Middle East, where extreme heat demands superior insulation, the Proof Max Combo Roofing System delivers by cutting energy waste by over 40% and offering top-notch waterproofing.
This makes it an ideal solution for both efficiency and cost-effectiveness.
Proof Max is dedicated to addressing key construction issues like water leakage and structural repair with innovative engineering solutions.
The Combo Roof System offers numerous benefits for both contractors and homeowners:
– Multi-layer system with both waterproofing and thermal insulation
– 25-year guarantee on performance
– Significant energy savings through reduced cooling costs
– No need for roof terrazzo tiles
– Single submittal and approval for the entire system
– High time efficiency during installation
These advantages make the Combo Roof System an excellent choice for durable, energy-efficient roofing solutions.
Combo Roofing System Process
A Combo Roof System is a comprehensive solution that integrates waterproofing layers, thermal insulation, and roof finishing.
- 1. Polyurethane Foam
- 2. Liquid Bitumen
- 3. Water Test
- Geotextile
- 5. Slope Lines
- 6. Screed
- 7. Skirting
- 8. Mastic Sealant
- 9. Cementitious Coating
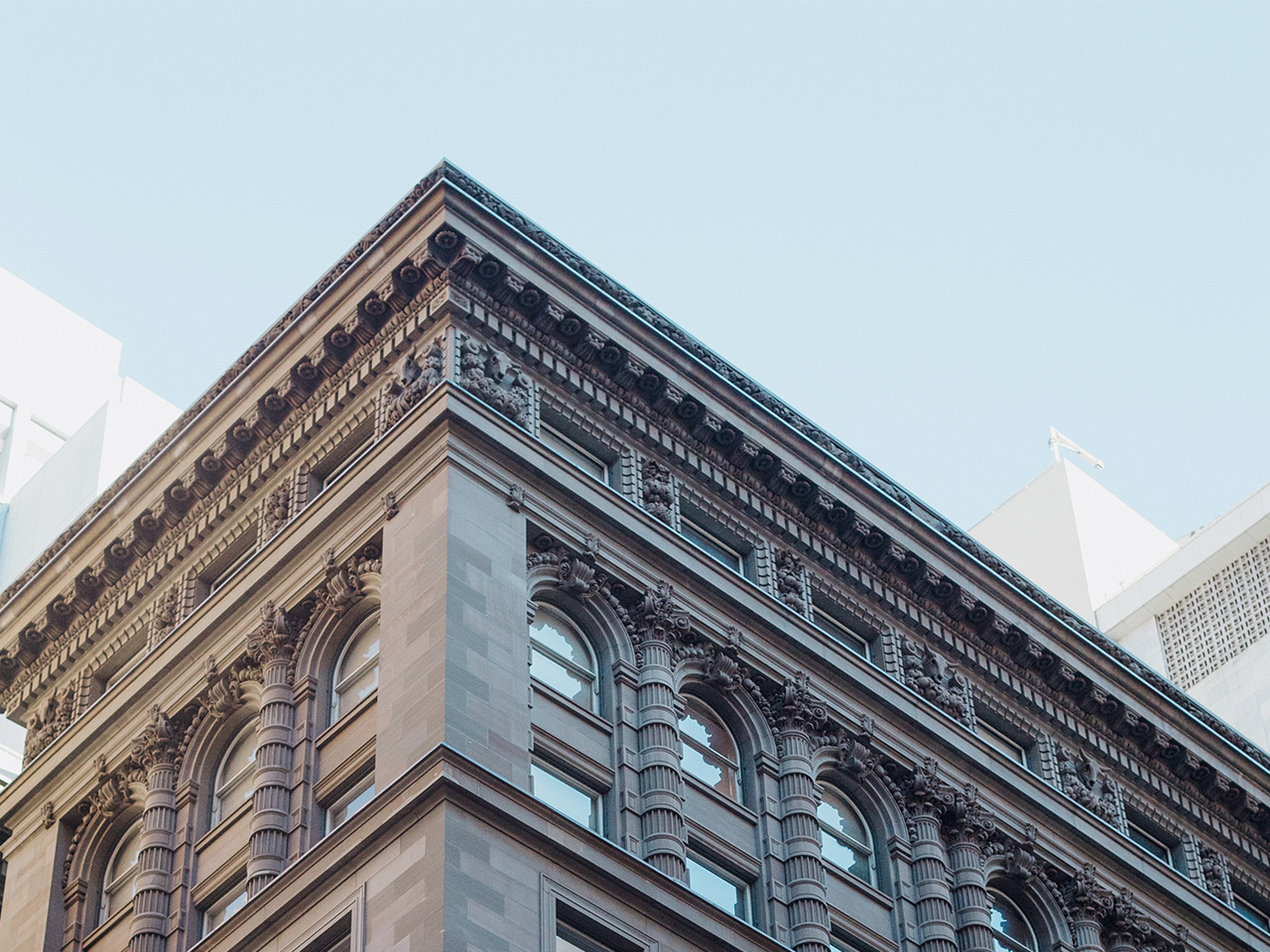
Call For a Quote:
+971 50 447 7980
Step Of Process
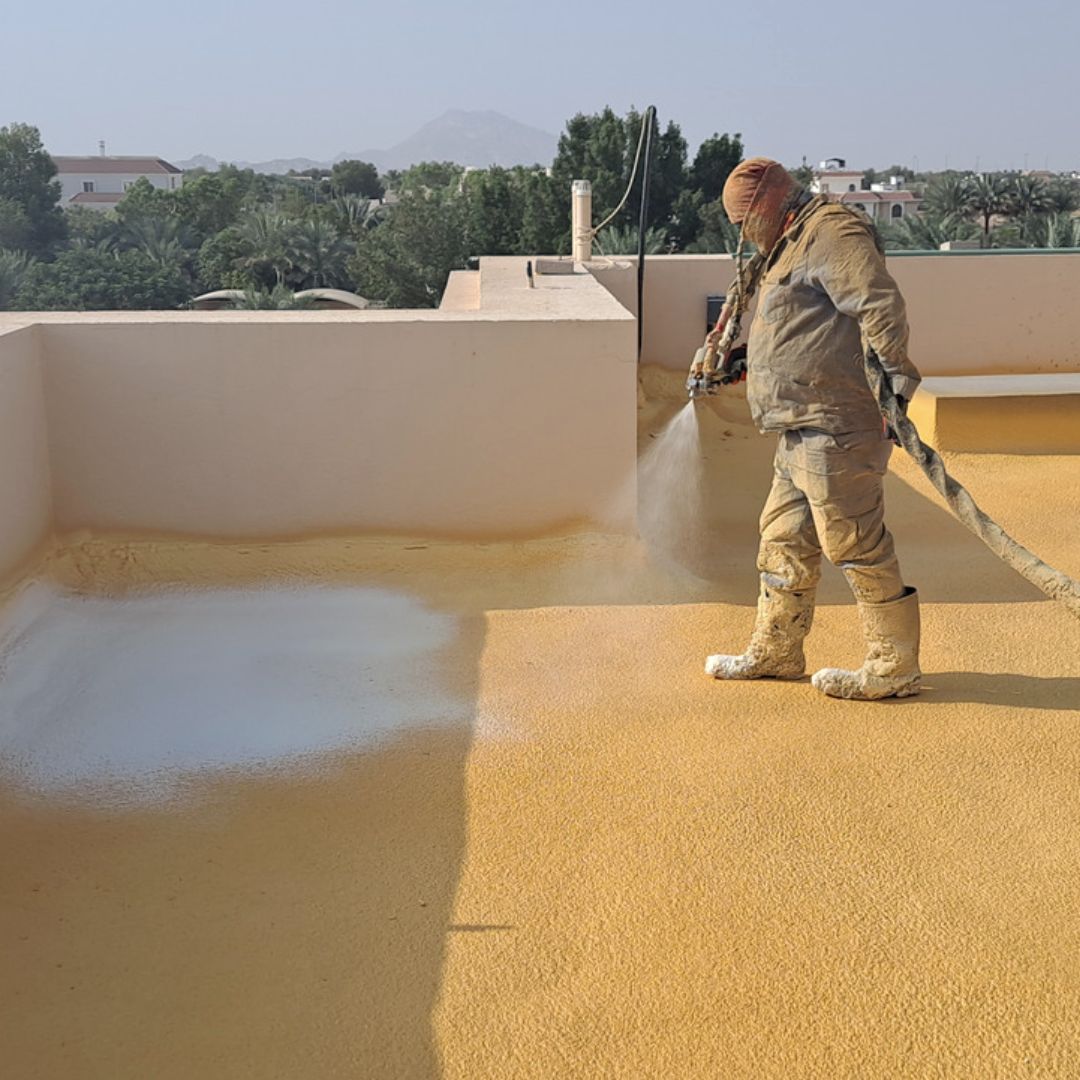
Polyurethane Foam
Spraying starts only after final inspection. Polyurethane materials, Polyol and Iso PMDI, are applied using a Spray Foam Machine. Spraying is done in layers until the desired thickness is achieved. A 45 kg/m³ polyurethane foam is sprayed on the clean rooftop, sealing cracks and edges. The foam solidifies in 30 seconds, forming a protective, waterproof layer. Each layer is 10-15 mm thick.
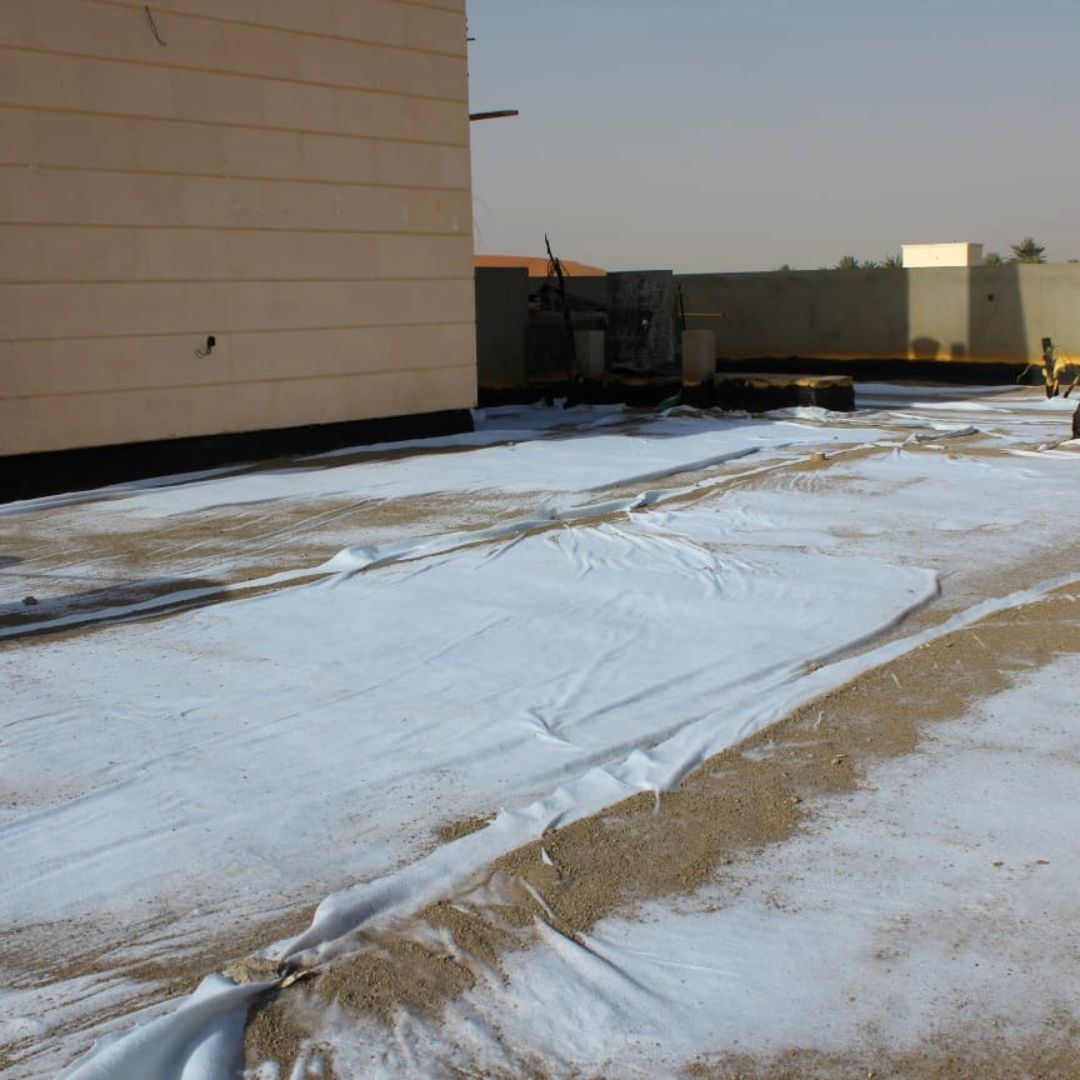
Geotextile
After an effective test, water will be taken out and one layer of geotextile will be approximately laid at a cover of 20 – 30 cm. The geotextile will be reached up to the vertical surface of the recently applied framework.
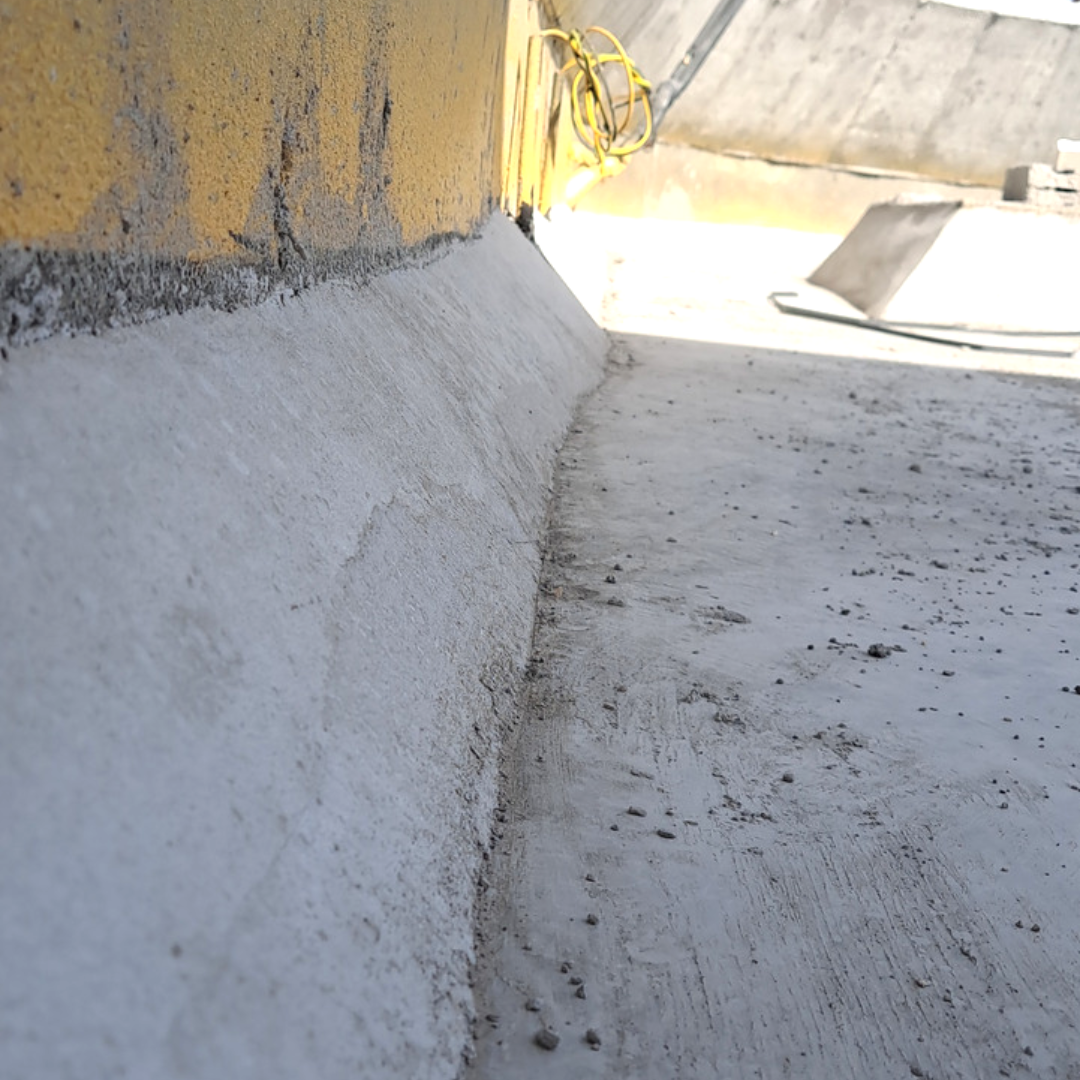
Skirting
Once the screed is fully cured, all joints formed by the Flexcell Board are opened and sealed with ACT sealant, using a 20mm backing rod to allow for concrete movement. Around the parapet skirting and foundations, a 100x100mm angle fillet is cut. The roof skirting is finished and protected with four layers:
1. Self-flashing polyurethane edges
2. Mortar for shape and strength
3. Fabric reinforcement with a bonding agent to prevent cracks
4. Acrylic coating as the final protective layer.

Liquid Bitumen
After applying the polyurethane foam, a single-layer acrylic-based elastomeric waterproof coating (RBE) is applied across the entire surface. Allow at least 8 hours for it to dry, depending on site conditions. To protect the polyurethane from UV damage, a 600-800 micron layer of fluid UV protective coating is then applied over the PU foam.
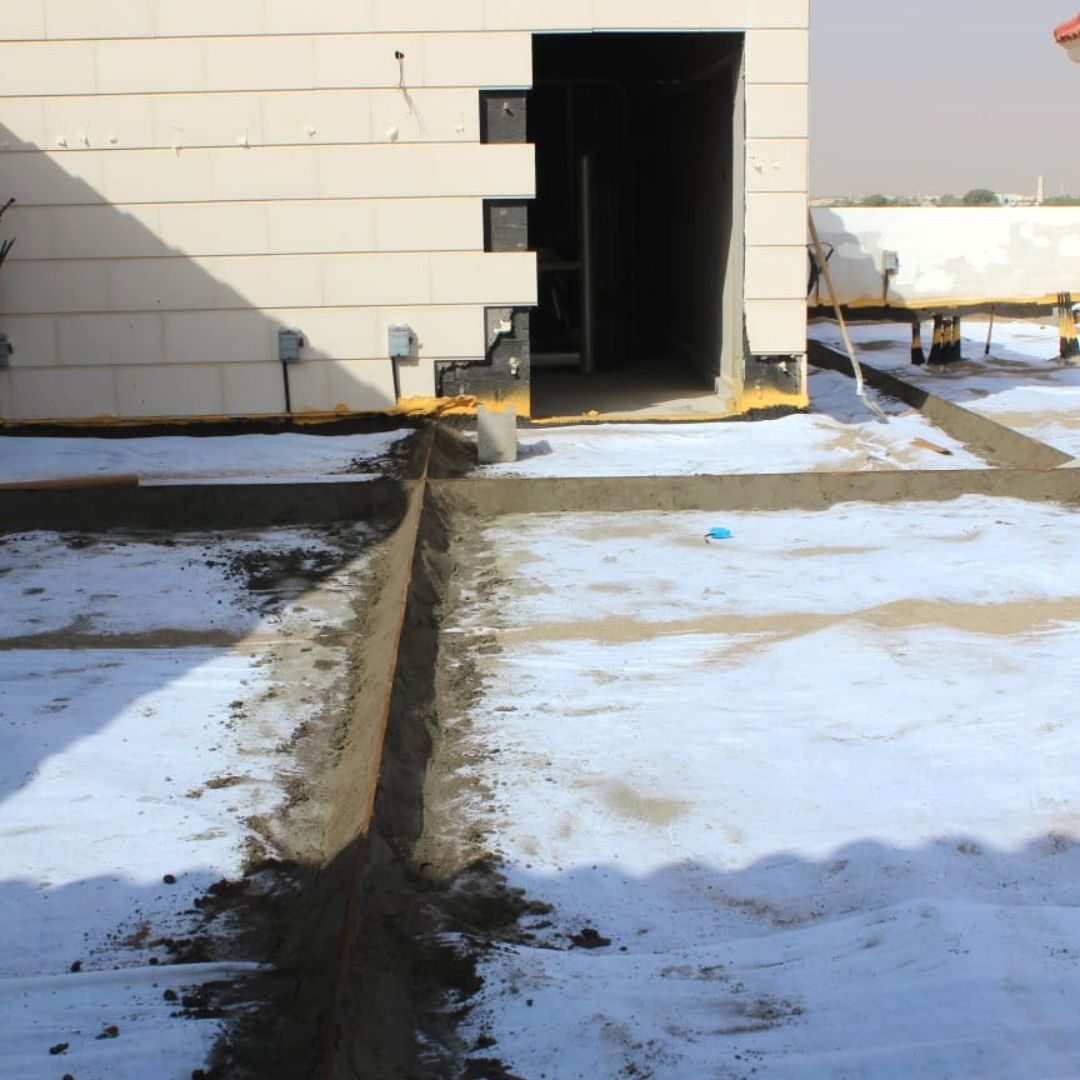
Slope Lines
After placing geotextile, the rooftop is divided into 3m x 3m sections with Compact Flexy Board for slope and expansion joints. A Rain Water Outlet is recommended for every 100 m². The roof is divided into rectangular or square sections of up to 6 m² using 12mm Flexcell Board and geotextile. Flexcell Board adjusts the slope, and sand concrete mortar is used to keep it vertical.
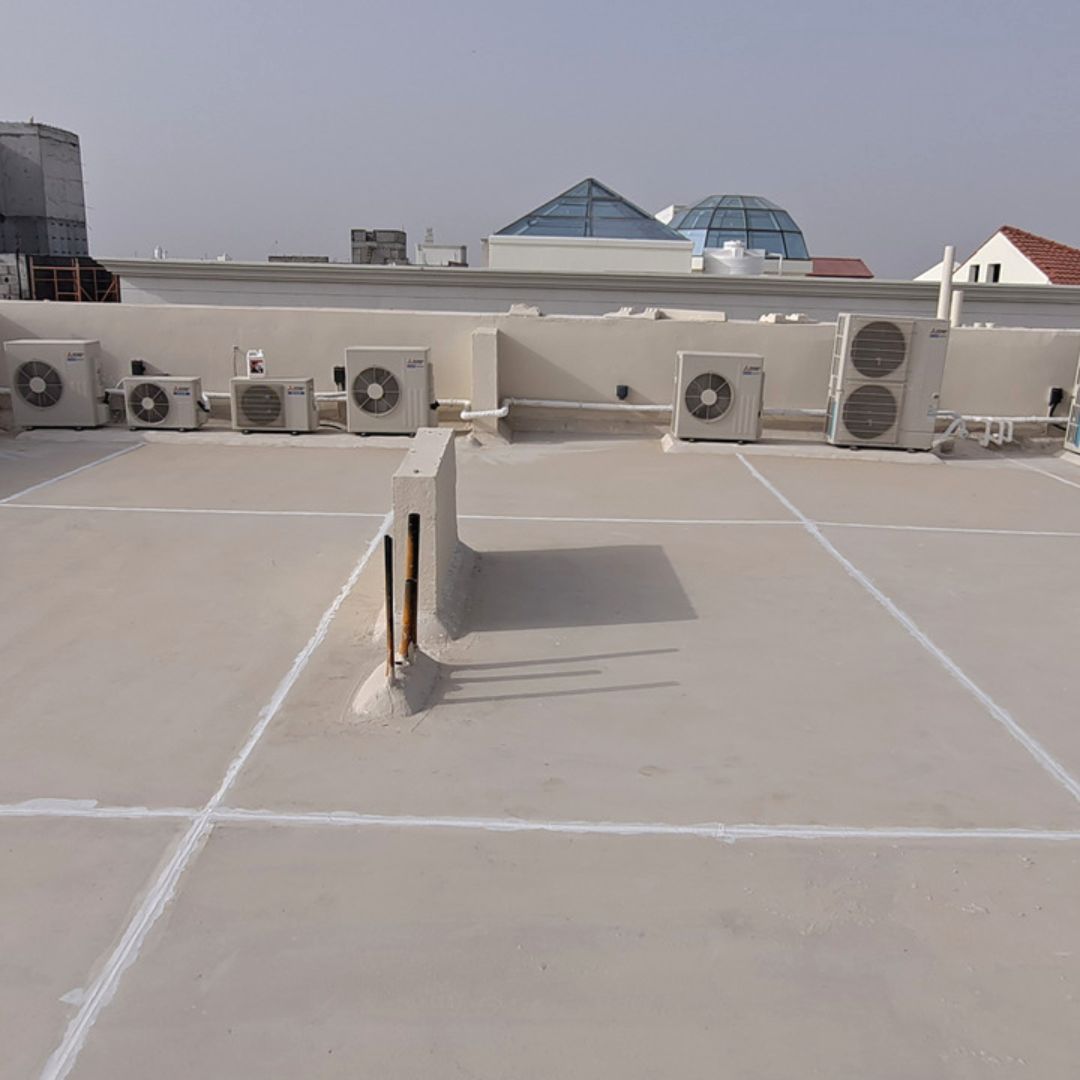
Mastic Sealant
Once the screed has been set, Compact Flexy board is cut from the top, a backing rod is installed, and sealant is applied to seal the expansion joints, giving your roof the best protection against leaks.
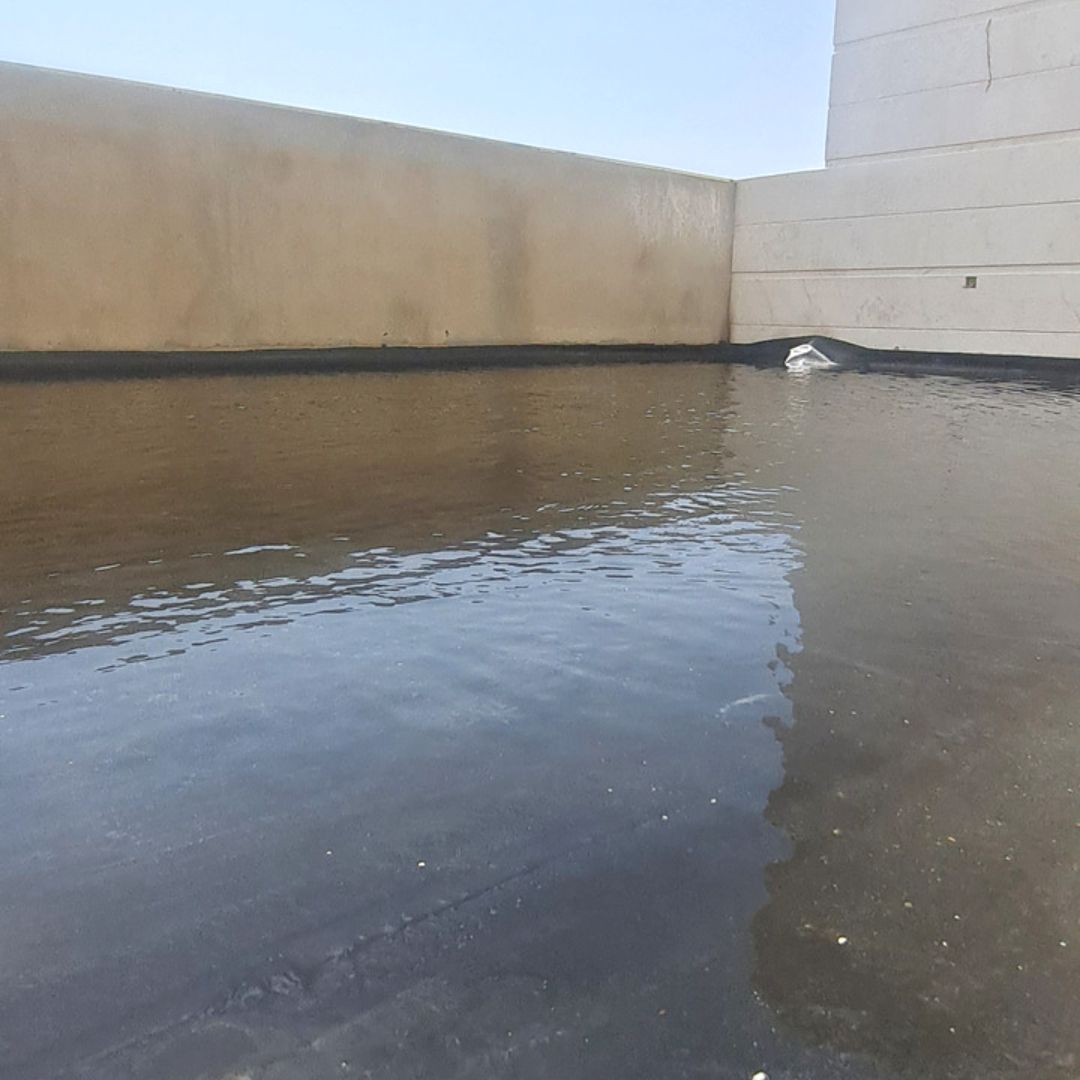
Water Test
After the UV covering has dried (at least 24 hours), a flood test with a water depth of 5-6 cm for 48 hours ensures no leakage in the framework. When the UV covering has completely dried, our engineer will visit the site to inspect the completed work and provide clearance for a flood test (at least 24 hours).
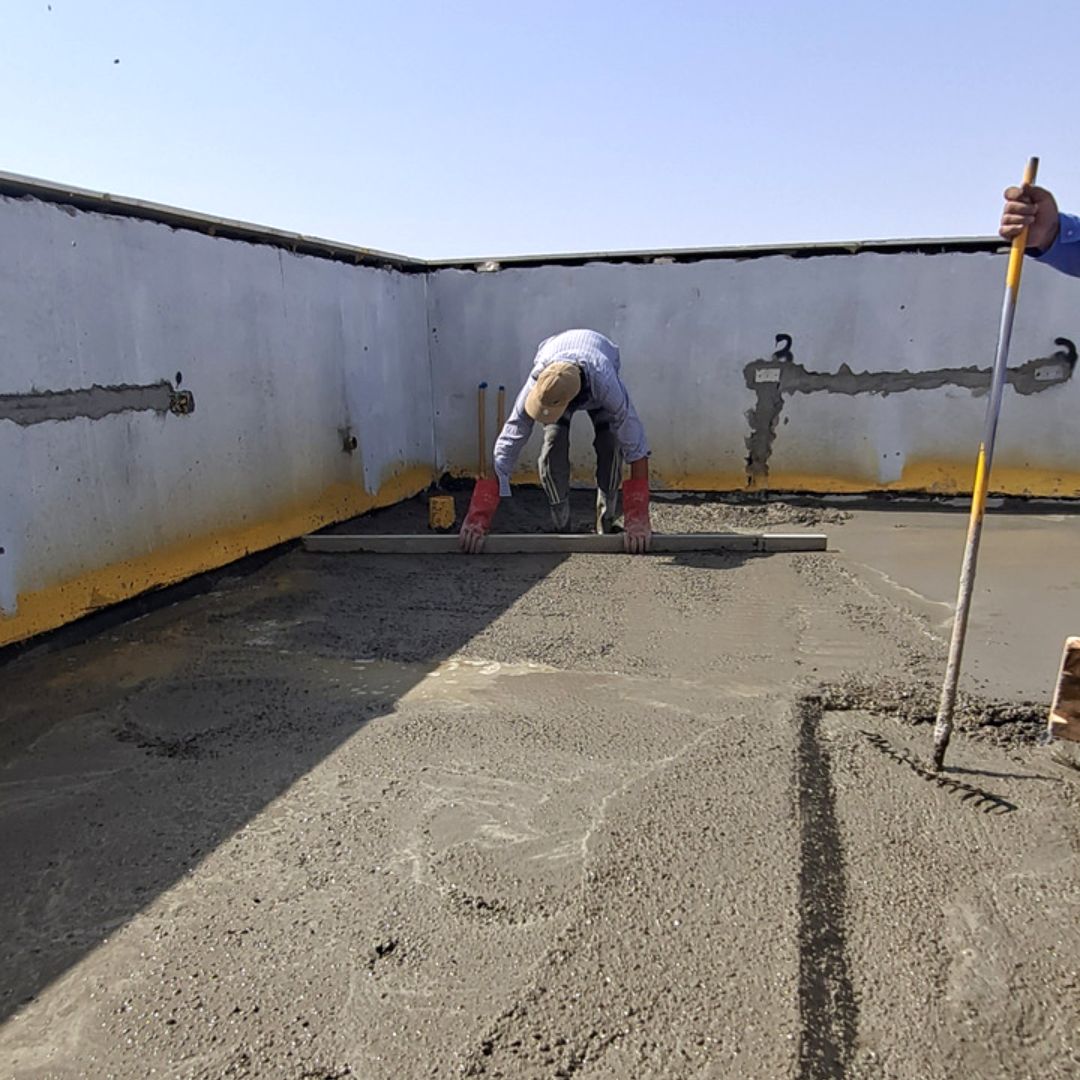
Screed
Once the Ridges are completed, our skilled masons will lay and level the screen to provide the perfect slope for a perfectly finished roof. To provide the best protection and minimal cracks, the screed is 20N/mm2, 250 OPC, 0.6 Kg/m3 Fiber-reinforced screed concrete. Following the paneling work, a protective screed with a strength of 20 N/mm2 will be laid in panels with an average screed thickness of 80mm. The screed will be finished smoothly and cured for two days (minimum).
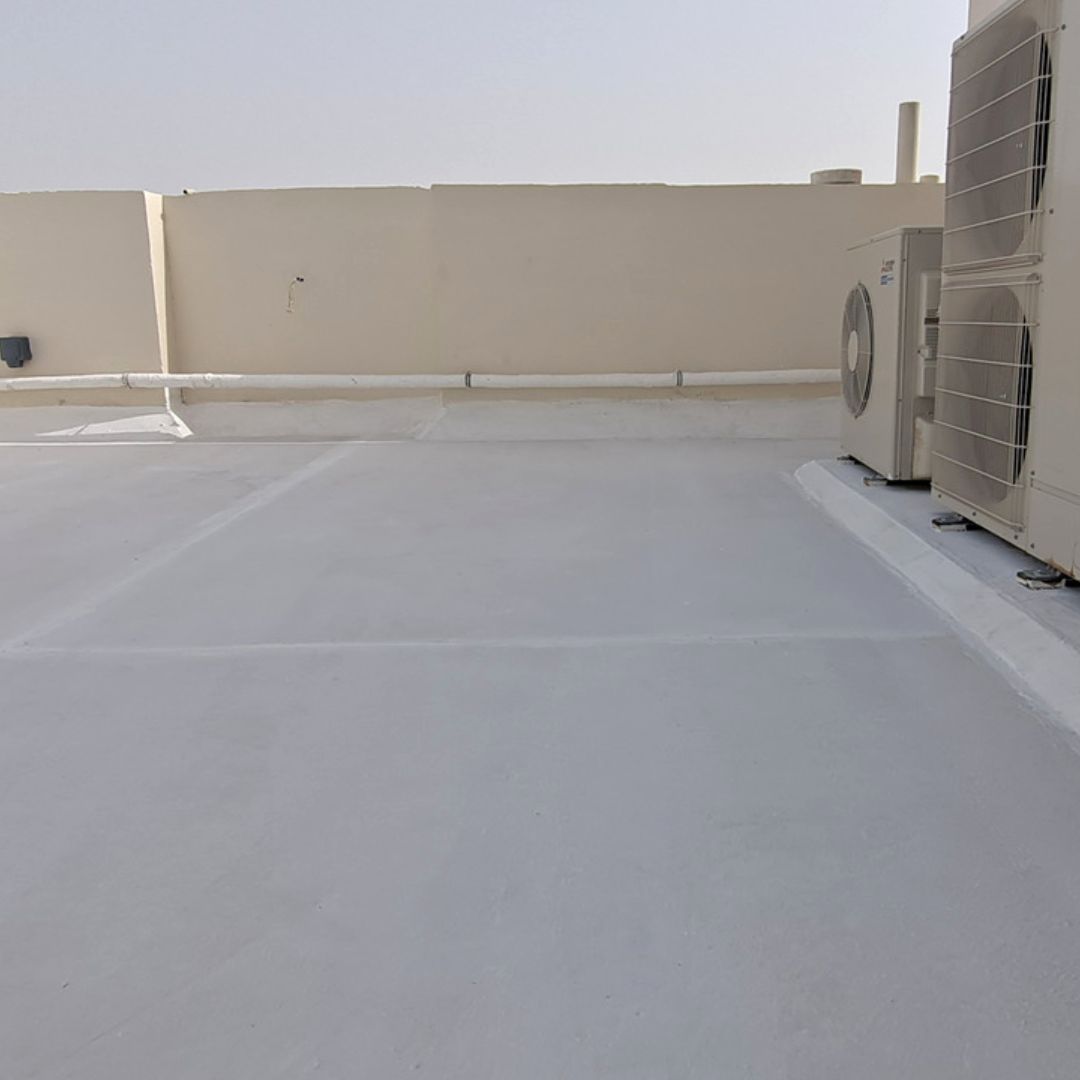
Cementitious Coating
Saturate the concrete surface with clean water after finishing the joint treatment, curing the applied angle fillet, and cast screed. To avoid dampness of the substrate, two coats of cementitious coating Polyflex (White) will be applied above the surface. Before allowing any traffic on the roof, the final coat will be allowed to fully cure for 7 days. The roof will look nice with the topcoat on it.
Get a Quote For Your Project
We’ve Been Building For Over 10 Years
We believe in affordability without compromising excellence, ensuring that everyone can access top-notch maintenance services.
Your satisfaction is not just a goal; it’s our promise. Choose Proof Max for a seamless blend of expertise, quality, and customer-centricity.
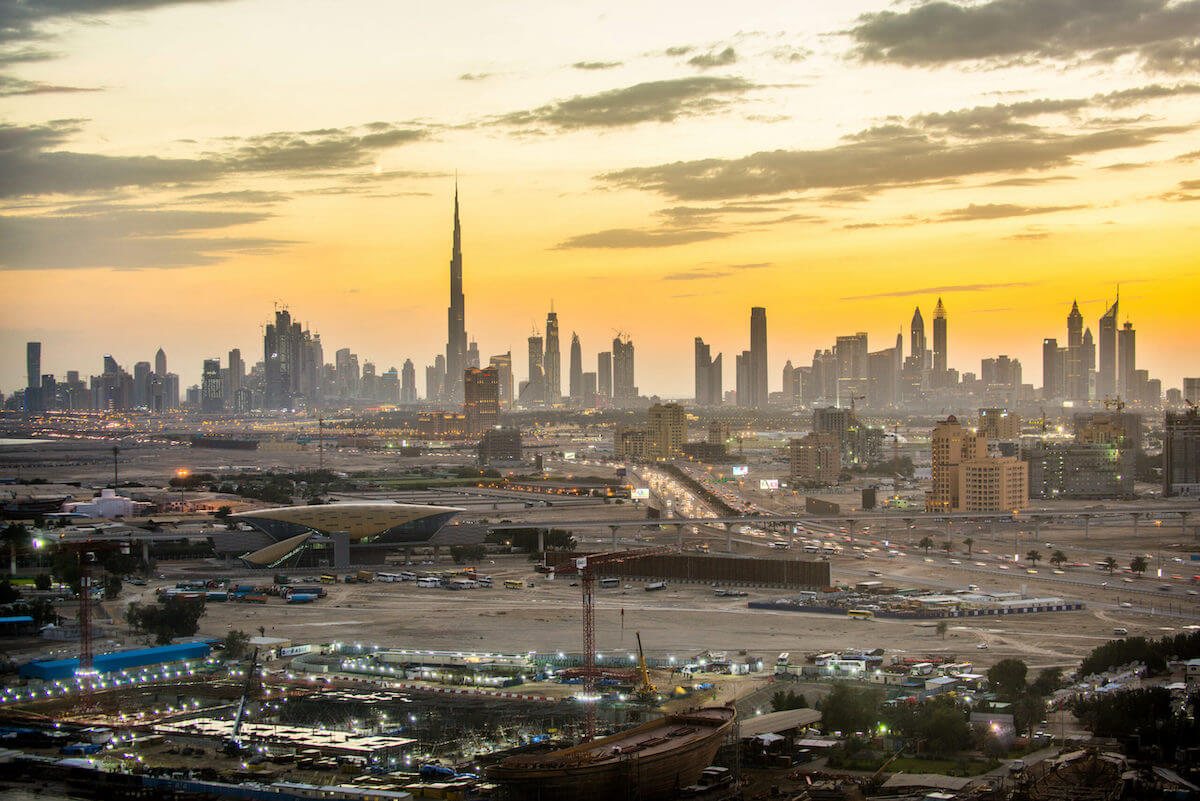
Call For a Quote:
+971 50 447 7980
Why choose us
Experienced and Qualified Team
Our team consists of highly skilled professionals who are experienced in their respective fields and have the qualifications to prove it.
High-Quality Workmanship
We use only the best materials and equipment for all our projects and are committed to providing top-notch services.
Affordable Pricing
We believe that quality maintenance services should be accessible to everyone,
which is why we offer competitive pricing without compromising on quality.
Customer Satisfaction Guaranteed
Our top priority is customer satisfaction, and we will do everything in our power to make sure you are happy with the results.